CNC Milling Parts: Precision Manufacturing for Applications
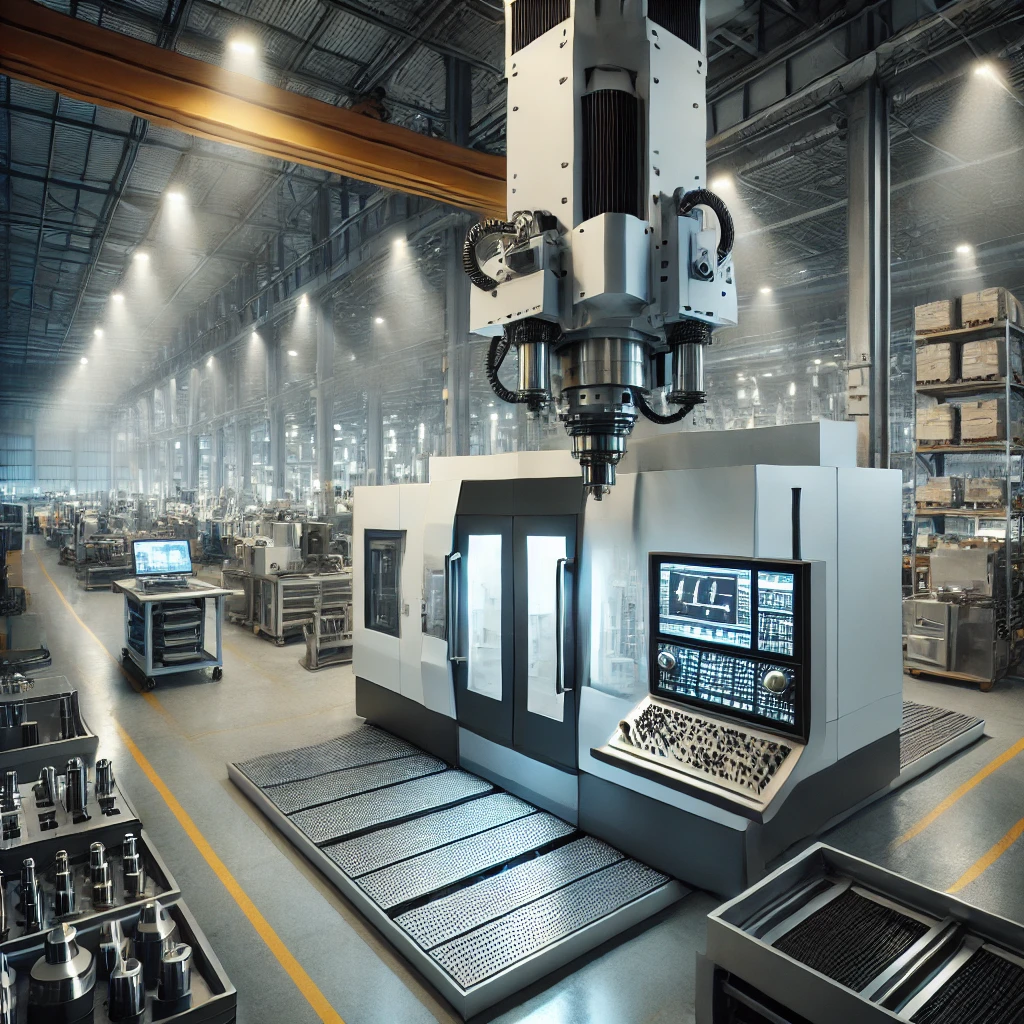
CNC (Computer Numerical Control) milling is a critical manufacturing process used to produce precise and complex parts for various industries, including automotive, aerospace, medical, and electronics. CNC milling parts are known for their accuracy, durability, and versatility, making them essential components in modern manufacturing. This article explores the benefits, applications, and key considerations of CNC milling parts, highlighting their importance in different industries.
Benefits of CNC Milling Parts
- High Precision and Accuracy
- Tight Tolerances: CNC milling machines can produce parts with extremely tight tolerances, ensuring precision and accuracy in every component.
- Consistent Quality: The use of computer-controlled processes ensures consistent quality across large production runs, minimizing defects and variations.
- Versatility
- Complex Geometries: CNC milling can produce intricate and complex geometries that are difficult to achieve with traditional manufacturing methods.
- Material Flexibility: CNC milling is compatible with a wide range of materials, including metals (aluminum, steel, titanium), plastics, and composites.
- Efficiency and Speed
- Automated Process: CNC milling is an automated process, reducing the need for manual intervention and increasing production efficiency.
- Quick Turnaround: Advanced CNC machines can quickly produce parts, meeting tight deadlines and reducing lead times.
- Cost-Effectiveness
- Reduced Waste: CNC milling minimizes material waste by precisely cutting and shaping parts, leading to cost savings.
- Scalability: The ability to easily scale production makes CNC milling cost-effective for both small and large batch production.
Key Applications of CNC Milling Parts
- Automotive Industry
- Engine Components: CNC milling is used to manufacture precise engine components such as cylinder heads, intake manifolds, and pistons.
- Transmission Parts: Critical transmission parts, including gears and shafts, are produced using CNC milling for high accuracy and durability.
- Custom Prototypes: CNC milling allows for the rapid prototyping of custom automotive parts, enabling design testing and validation.
- Aerospace Industry
- Structural Components: CNC milling is essential for creating structural components of aircraft, including wing ribs, fuselage frames, and landing gear parts.
- Turbine Blades: The precision required for turbine blades in jet engines is achieved through CNC milling.
- Spacecraft Parts: CNC milling produces high-precision parts for spacecraft, ensuring reliability and performance in extreme conditions.
- Medical Industry
- Implants and Prosthetics: CNC milling is used to create custom implants and prosthetics, ensuring a perfect fit and biocompatibility.
- Surgical Instruments: Precision surgical instruments, including scalpels, forceps, and clamps, are manufactured using CNC milling.
- Diagnostic Equipment: CNC milling produces components for diagnostic equipment, ensuring accuracy and reliability.
- Electronics Industry
- PCB Prototyping: CNC milling is used to prototype printed circuit boards (PCBs), allowing for rapid testing and iteration.
- Enclosures and Housings: CNC milling creates custom enclosures and housings for electronic devices, ensuring protection and functionality.
- Connector Components: Precision connectors and interconnect components are produced using CNC milling for high-performance electronic assemblies.
- Industrial Machinery
- Machine Parts: CNC milling produces various machine parts, including gears, cams, and shafts, ensuring durability and precision.
- Tooling: CNC milling is used to manufacture tooling components such as molds, dies, and jigs, essential for production processes.
- Automation Equipment: Components for automation equipment, including robotic arms and conveyor systems, are manufactured using CNC milling.
Key Considerations When Choosing CNC Milling Parts
- Material Selection
- Compatibility: Ensure the material chosen is compatible with the CNC milling process and meets the required specifications for strength, durability, and performance.
- Application Needs: Consider the specific needs of the application, including environmental conditions, load requirements, and thermal properties.
- Tolerance and Precision
- Required Tolerances: Define the required tolerances for the part to ensure precision and fit within the assembly.
- Inspection and Quality Control: Implement rigorous inspection and quality control measures to maintain consistency and accuracy.
- Design and Complexity
- Complex Geometries: Take advantage of CNC milling’s ability to produce complex geometries, optimizing part design for performance and functionality.
- Design for Manufacturability: Ensure the design is optimized for CNC milling, reducing production time and costs.
- Surface Finish
- Finish Requirements: Specify the required surface finish for the part, considering factors such as smoothness, texture, and appearance.
- Post-Processing: Determine if additional post-processing steps, such as polishing or coating, are needed to achieve the desired finish.
- Production Volume
- Batch Size: Consider the production volume and batch size, ensuring the CNC milling process is cost-effective for both small and large runs.
- Lead Time: Assess lead time requirements and choose a CNC milling service that can meet production deadlines.
Leading CNC Milling Services
- Xometry
- Overview: Xometry provides on-demand manufacturing services, including CNC milling, with quick turnaround times and competitive pricing.
- Capabilities: They offer a wide range of materials and finishes, ensuring high-quality parts for various applications.
- Quality Assurance: Xometry ensures rigorous quality control and inspection processes.
- Protolabs
- Overview: Protolabs specializes in rapid manufacturing, offering CNC milling services with a focus on speed and precision.
- Material Options: They provide an extensive selection of materials, including metals and plastics, to meet diverse needs.
- Customer Support: Protolabs is known for excellent customer support and detailed online resources.
- Fictiv
- Overview: Fictiv offers a digital manufacturing platform connecting clients with a network of vetted CNC milling partners.
- Flexibility: They provide flexible manufacturing solutions, from prototyping to large-scale production.
- Quality Control: Fictiv maintains strict quality control measures to ensure high-quality parts.
- Hubs
- Overview: Hubs (formerly 3D Hubs) offers on-demand CNC milling services with a global network of manufacturing partners.
- Transparency: Their online platform provides transparent pricing and real-time order tracking.
- Customization: Hubs offers extensive customization options to meet specific project requirements.
- RapidDirect
- Overview: RapidDirect provides comprehensive CNC milling services with a focus on precision and fast delivery.
- Capabilities: They offer various CNC milling options, including multi-axis machining, for complex parts.
- Support: RapidDirect offers technical support and design assistance to optimize manufacturing processes.
Conclusion
CNC milling parts play a crucial role in modern manufacturing, offering precision, versatility, and efficiency across various industries. By understanding the benefits, applications, and key considerations, businesses can leverage CNC milling to produce high-quality parts that meet their specific needs. Leading CNC milling services like Xometry, Protolabs, Fictiv, Hubs, and RapidDirect provide comprehensive solutions to ensure the successful production of CNC milled components.